La Ducati Monster è uno dei modelli più iconici della casa motociclistica bolognese, considerato il capostipite delle moto “naked”, con propulsore in bella vista. Un concentrato di stile, sport e tecnologia: negli anni, abbiamo scelto proprio questo modello per mettere alla prova i nostri reparti nella progettazione, sviluppo e produzione digitale di componenti aftermarket personalizzati. È così che è nato J-Monster, che sin dai nostri primi albori esponiamo agli eventi e rinnoviamo periodicamente con nuovi componenti, utilizzando le tecnologie più moderne, a scopo dimostrativo.
J-MONSTER: MOLTO PIÙ DI UN ESERCIZIO DI STILE
La possibilità di condividere con il pubblico quello che facciamo è spesso una criticità per noi. Siamo legati con i nostri clienti con contratti di riservatezza, visto che i prodotti a cui lavoriamo potrebbero uscire sul mercato anche diversi anni dopo il nostro contributo nella fase di ricerca e sviluppo.
J-Monster è un esempio perfetto di come si svolge il lavoro quotidiano in Juno: siamo attivi al fianco del cliente, attingendo all’esperienza trasversale dei nostri reparti per proporre soluzioni fuori dagli schemi; ogni giorno sfruttiamo le più classiche competenze di design e progettazione combinandole con le nuove possibilità offerte dall’Additive Manufacturing e dalla stampa 3D.
Il progetto ha coinvolto la divisione R&D per la cura del reverse engineering ed il rilievo delle geometrie, la divisione DESIGN per lo stile delle superfici e la divisione 3D PRINT per la produzione dei componenti.
ELEMENTI CUSTOM PER MOTOCICLETTE: ESTREMI NELLE PRESTAZIONI, UNICI NELLO STILE.
Carbon Digital Light Synthesis™ ha introdotto la possibilità di utilizzare polimeri estremamente performanti, con eccellenti caratteristiche meccaniche, alta precisione nella riproduzione delle texture ed una qualità superficiale impeccabile.
La tecnologia è quindi perfetta per realizzare componenti che devono necessariamente resistere ad alte temperature e forti sollecitazioni meccaniche, come il copri marmitta anteriore e posteriore, manopole e cuscinetti.
Il materiale EPX 82 è stato impiegato per i copri marmitta.
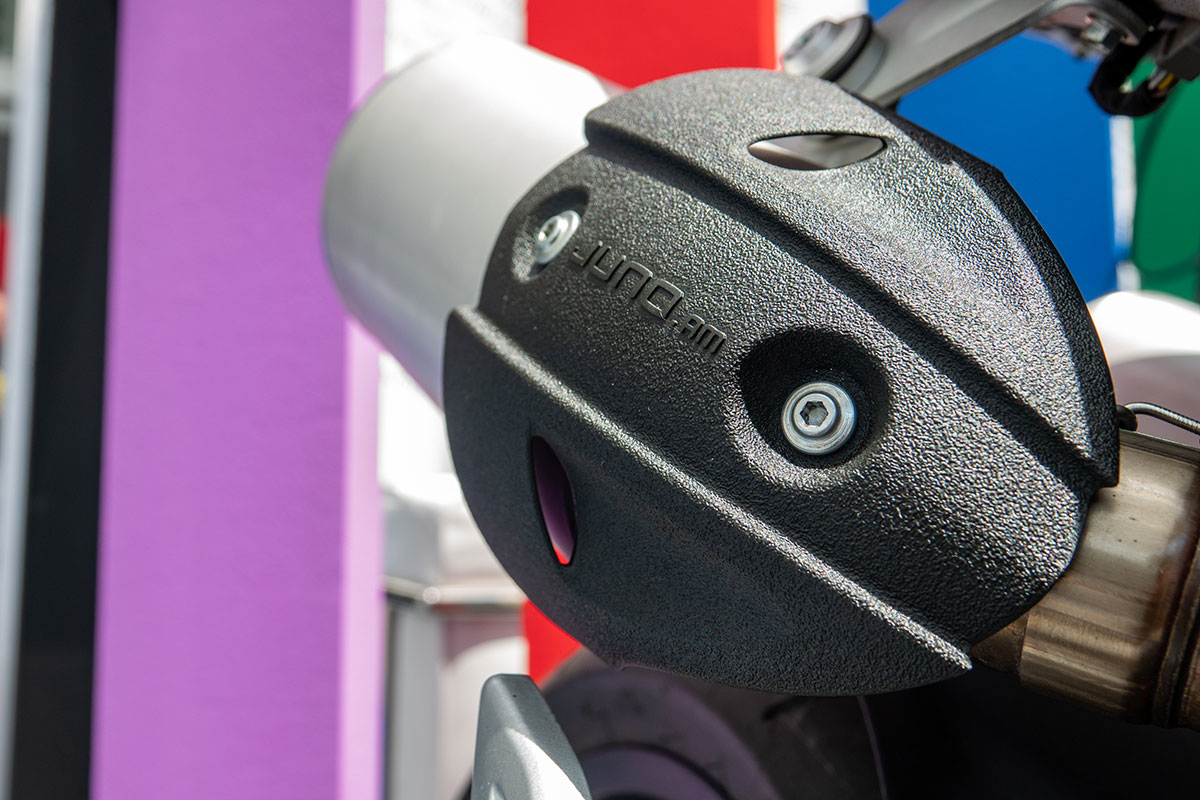
Si tratta di un materiale termoplastico comparabile ai caricati vetro, resistente ai raggi UV e perfetto per evitare che le parti soffrano cambiamenti d’aspetto, perdita di colore o subiscano la formazione di crepe dovute all’esposizione prolungata al sole.
Questo elastomero è noto anche per essere utilizzato da Lamborghini per componentistica su Urus e Sian.
Il materiale presenta inoltre un’ottima resistenza chimica, adatta a sopportare a sversamenti di carburante, e un’eccellente resistenza termica (oltre i 180° C, anche nel caso di fiamma viva): si tratta di una caratteristica ottimale vista la posizione dei copri marmitta vicino al terminale. La resistenza termica può essere ulteriormente aumentata optando per il CE 221, in grado di sopportare temperature oltre i 230° C.
Oltre agli aspetti prettamente funzionali, i componenti aftermarket personalizzati richiedono di rispettare i dettami estetici tipici della customizzazione: si tratta di combinare esigenza tecnica e gusto del cliente. Anche in questo la stampa 3D industriale, e la tecnologia Carbon in particolare, sono una scelta ottimale.
Con le tecnologie di produzione tradizionali, le texture superficiali dei componenti vengono tipicamente realizzate tramite agenti chimici applicati sulla matrice in acciaio; segue che lo schema grafico e la finitura sono le stesse per ogni pezzo del lotto produttivo.
La stampa 3D permette invece di arrivare alla personalizzazione anche del singolo elemento e, non richiedendo attrezzature di supporto alla produzione, rende possibile realizzare anche piccole quantità di pezzi con texture diversificate.
Essendo possibile una variazione digitale direttamente da file, è inoltre possibile collocare altri elementi di stile in modo molto più semplice rispetto ad un classico stampo o ad altre tecnologie produttive tradizionali; inserire un logo, il nome del proprietario o anche l’identificativo della versione speciale del prodotto diventano operazioni prive di complessità.
STRUTTURE LATTICE: ESTETICA NELLE FORME, COMFORT PER IL PILOTA
Una caratteristica che ben coniuga funzionalità ed estetica è l’impiego di strutture lattice.
Estremamente complesse da generare, presentano un pattern costituito da un reticolo ripetuto in sequenza; su J-Monster sono state utilizzate per il cuscinetto e per i paramani.
Le strutture lattice sono particolarmente leggere e, oltre ad offrire un indubbio impatto estetico, possono essere modulate per rispondere al meglio ai carichi compressivi e impulsivi.
I cuscinetti custom sono situati nella zona dove il motociclista preme il ginocchio mentre è in piega ed in corrispondenza dell’appoggio addome sul serbatoio: il materiale e la struttura lattice garantiscono sia un comfort ottimale che forme assolutamente originali.
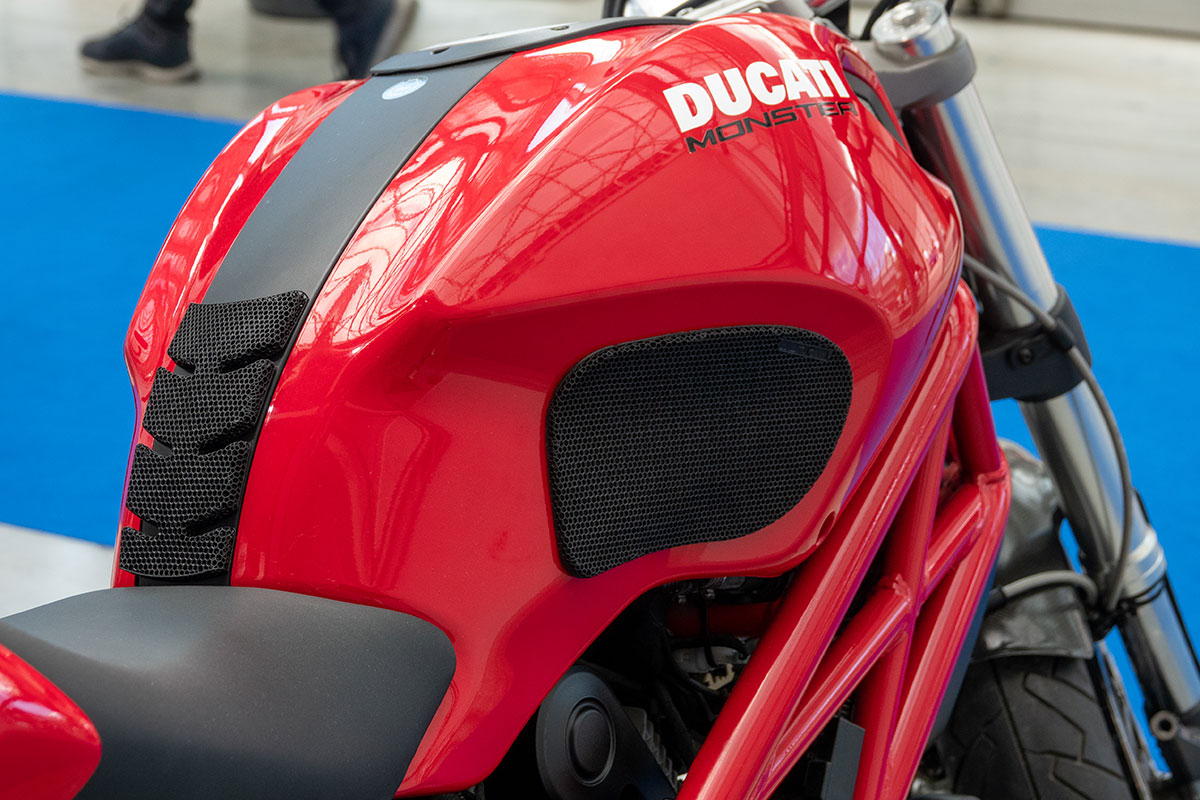
In quanto partner del Carbon Network, Juno può accedere al Carbon Design Engine, un software che permette di generare la struttura lattice anche da file solido in modo tale che sia già perfettamente adeguata alla stampa con Carbon.
Il materiale scelto per l’elemento è l’elastomero bicomponente EPU 40.
Mentre per piccole tirature l’EPU 40 risulta una scelta eccellente, quando si passa alla produzione è conveniente valutare l’uso di materiali simili come EPU 41: simile nelle prestazioni, ma che può meglio adattarsi ad una ottimizzazione del lotto produttivo di migliaia di pezzi. Questi elastomeri sono noti anche per essere utilizzati da Adidas per le iconiche scarpe Futurecraft 4D.
Entrambi i materiali fanno parte della famiglia di elastomeri poliuretanici, con caratteristiche sia meccaniche che chimiche del tutto comparabili alle gomme vulcanizzate.
Si tratta di materiali A+B che vengono catalizzati già prima della produzione e trattati termicamente dopo la stampa con un ciclo di 12 ore in forno (con un processo simile alla vulcanizzazione tradizionale).
Il risultato è un materiale estremamente resistente e performante.
Focus on: gomma Carbon o gomma Polyjet?
![]()
La gomma ottenibile tramite tecnologia di stampa 3D Polyjet sopporta temperature fino ai 40-50°C, è solo fotopolimerizzata e non comparabile alle vulcanizzate, offre una resistenza a rottura mediamente bassa.
Con Polyjet è possibile realizzare superfici che trasmettono esattamente la sensazione al tatto del prodotto finito. Si tratta di un’ottima soluzione per la prototipazione, ad esempio, di test di ingombro o prototipi concettuali (anche multicolore o a durezza variabile da 30ShA fino a 95ShA) estremamente realistici perché permette l’abbattimento di costi e tempi anche per un singolo pezzo: poche ore sono sufficienti per ottenere un prototipo pronto per essere provato ed i prezzi sono più bassi per via dell’assenza dei costi di avvio fissi che possiamo trovare nella DLS.
La tecnologia introdotta da Carbon e l’ampia gamma di materiali, pur essendo adatta anche a scopi prototipali, presenta costi di laboratorio più elevati ed è la soluzione ideale in caso di produzioni che prevedono un maggior numero di pezzi oppure quando si desidera un prototipo del tutto identico, per prestazioni e materiale, a quello che sarà il prodotto finito.
STAMPA 3D DEL METALLO: ELEMENTI SICURI ED OMOLOGABILI
La stampa 3D metallo – tecnologia DMLS – è ciò che abbiamo scelto per realizzare il pedalino
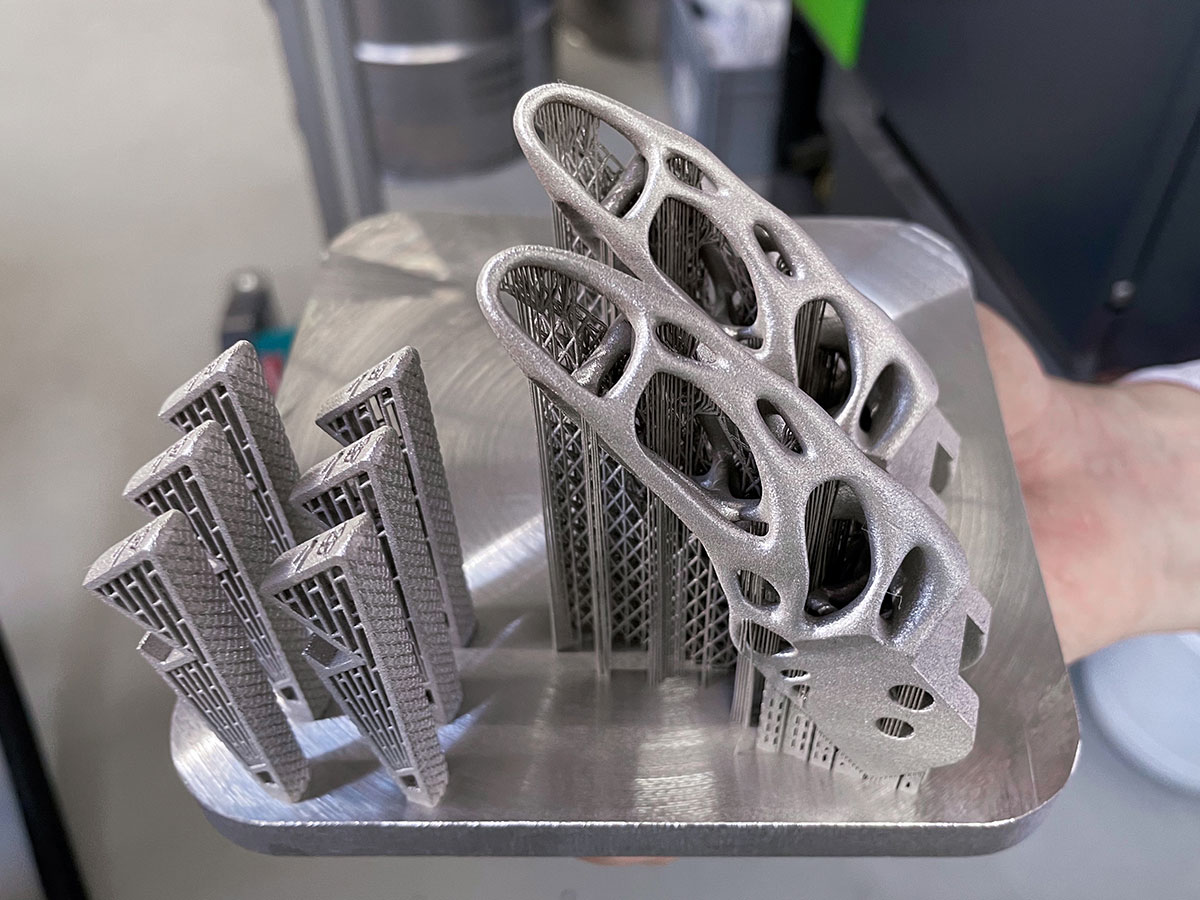
La tecnologia industriale di stampa 3D del metallo permette di ottenere pezzi completamente funzionali con proprietà meccaniche e termiche pari a quelle di un pezzo ottenuto dal pieno o da fusione o addirittura superiori. DMLS significa poter coniugare la libertà delle forme caratteristica delle stampa 3D alle tipiche operazioni svolte sui metalli in officina o nel laboratorio analisi.
Il pezzo definitivo realizzato tramite tecnologia DMLS può tranquillamente subire trattamenti termici o di HIPping, essere forato, alesato, saldato, ecc.
Questo pedalino potrebbe essere anche omologabile su moto da strada, e non limitato a modelli da pista o ai prototipi.
RAPID JUNO MOLDING: STAMPI TRAMITE ADDITIVE MANUFACTRING
In Juno lavoriamo regolarmente non solo con le più moderne tecnologie di stampa 3D, ma anche con metodi produttivi più tradizionali.
Per il parafango, il puntale e la presa d’aria sul serbatoio qualche anno fa avevamo scelto la fibra di carbonio e seguito questo processo:
Abbiamo anche depositato un brevetto per la realizzazione di stampi tramite additive manufacturing, il “Rapid Juno Molding”, il cui obiettivo è velocizzare la produzione degli stampi, rispondendo all’urgenza tipica di settori estremi come il motorsport.
La rapidità nel portare aggiornamenti è spesso ciò che fa la differenza in gara e Rapid Juno Molding permette di realizzare componenti in fibra di carbonio in pochissimi giorni.
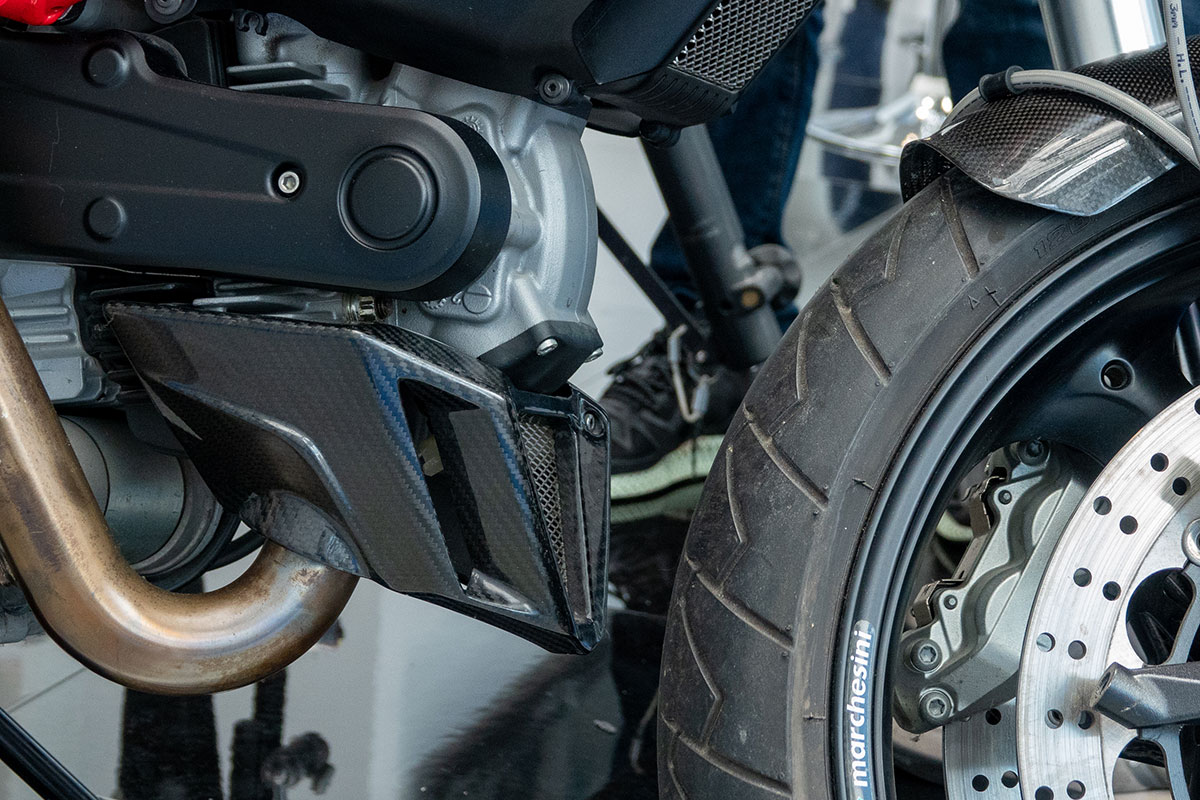
Visto e piaciuto il nostro progetto già pronto, Ducati stessa ci ha acquistato stampo e modello di design del puntale così da poter inserire quest’ultimo elemento nel catalogo Ducati Performance, dedicato agli accessori speciali. Il mercato della componentistica aftermarket, in ambito automotive e racing è sempre stata per noi parte importante del business, piccole officine o anche noti brand specializzati.
Anche le grandi aziende trovano, non di rado, importanti vantaggi nelle competenze trasversali che nei reparti di Juno operano in perfetta sinergia: trovano una risposta pronta, efficiente ed efficace per ottimizzare l’organizzazione delle risorse interne ed a lanciare sul mercato anche un progetto completo.
METODO JUNO: ITERARE FINO A RAGGIUNGERE LA PERFEZIONE
Juno è estremamente flessibile, elastica e reattiva.
Aziende di ogni dimensione possono fare affidamento sul nostro know-how e sull’esperienza trasversale delle nostre divisioni per consulenza e affiancamento, dal progetto alla produzione, o per risolvere emergenze e picchi di lavoro: la flessibilità che ci caratterizza ci permette di lavorare 7 giorni su 7 adattandoci rapidamente a processi, tempi e metodi dei nostri clienti, permettendo loro di raggiungere gli obiettivi prefissati in modo rapido ed efficace.
Le divisioni 3D Print, R&D e Design operano in modo coeso e coerente nello stesso ambiente di lavoro, con feedback rapidi e puntuali anche in caso di progetti complessi, per i quali Juno diventa un vero e proprio partner che affianca il cliente, passo dopo passo.
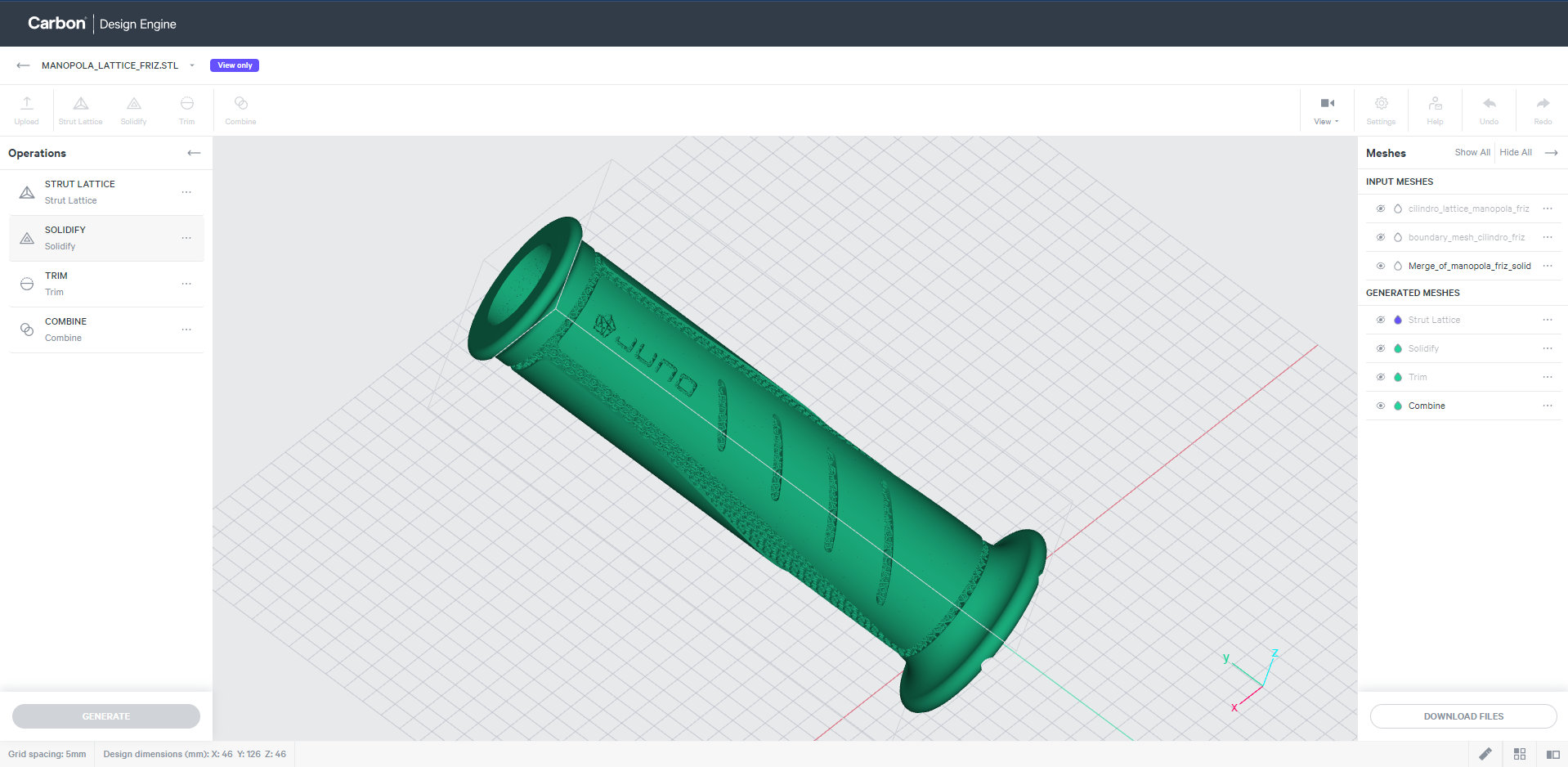
La nostra storia inizia dagli anni ’80, dallo Studio Pedrini, dalla capacità, impressa a fuoco nel nostro DNA, di affiancarci ai progettisti comprendendo le finalità del progetto; questo ci consente di mettere a disposizione decenni in cui le ideazioni hanno preso forma, sono state prototipate e sono state prodotte in serie anche utilizzando la stampa 3D come driver di innovazione ed accelerazione.
La profonda padronanza dei software CAD è la naturale conseguenza di un processo che storicamente mette cliente e progetto al centro di una costellazione di opportunità. Annoveriamo nello staff disegnatori specializzati nei diversi software di disegno e possiamo quindi supportare, nativamente e senza formati di interscambio, Creo Parametric, SolidWorks, Inventor, Rhinoceros, Geomagic e gli altri programmi tipicamente adottati dai designer.
Il nostro know-how in design, progettazione e produzione ci impone di non accontentarci di un risultato parziale: iteriamo, insieme al cliente, perché ogni dettaglio rispecchi le sue ambizioni e i suoi desideri.
BOLOGNA: LA MOTOR VALLEY ED I PROTAGONISTI DEL FUTURO
Bologna è capoluogo dell’Emilia-Romagna. Si trova in posizione strategica tra Firenze e Milano ma, soprattutto Bologna è nel bel mezzo della Motor Valley, il distretto industriale dove sono nate ed hanno sede alcune delle industrie automobilistiche e motociclistiche più note al mondo.
Si tratta di una regione dove, storicamente, le competenze nelle discipline della meccanica e dalla progettazione sono forti e radicate e dove scuole e istituti di formazione preparano ogni giorno i talenti per il futuro.
Coltiviamo talenti e competenze (anche in progetti a forte innovazione) mettendo in relazione esperienza e voglia di essere protagonisti del futuro adottando e sperimentando tecnologie, come la stampa 3D industriale, che offrono potenzialità del tutto inesplorate.
Estendiamo questa passione nel guardare il domani anche ai clienti, che possono contare su un partner che ha solide radici ma che ricerca, con costanza, la direzione verso la quale i naturali mutamenti industriali saranno condotti.