The decision to adopt additive manufacturing technologies was not dictated by a desire to follow a market trend: it stemmed from the urge to keep expanding and innovating the experience Studio Pedrini has gained in more than 25 years of designing, developing and industrializing products for its clients.
In 2007, Stratasys' first Polyjet 3D printing system was installed, an example of resin 3D printing that, with the proper hardware and software upgrades, is still fully suited for the production of aesthetic and functional models.
Providing additive manufacturing services for Studio Pedrini's projects, for such cross-cutting needs and goals, inevitably required investing time to increase and stabilize reliability. The independent company Juno Design was established 5 years after the installation of the first printer, 5 years that were partly spent in the search for disruptive solutions, but primarily in fine-tuning processes to ensure quality consistency.
Ten years is a milestone that shows the trust placed in us. At the same time, ten years represent a landmark in terms of our maturity as well as that of the industry: AM technologies enable not only prototyping but also manufacturing, with results matching those of other established manufacturing technologies in terms of quality.
Our first 10 years have gone by in the blink of an eye and are the foundation for the next 10 years, which we are sure will be just as complex and challenging; most of all, they will show us how far contemporary designers will take their ideas
.
What happened in the 3D printing sector?
We now use sophisticated, high-performance industrial 3D printing systems that can guarantee excellent repeatability, but how did it all begin?
As of today, it has been 10 years since the formal opening of the spin-off. 10 years that actually started a little earlier.
Sometime around 2010, the 2 printers above made their appearance. They were iconic in their own way and witnesses to a pioneering stage in which a great deal was still to be explored, but also to a moment when people wanted to make their best to leave the financial crisis of 2008 behind them.
The Designjet 3D Printer by HP was probably the first step of the multinational corporation into the additive manufacturing sector. A printer using filaments, which was functional, but sure a far cry from the ambitions of HP; several years later, the corporation would invade the market with the revolutionary Multi Jet Fusion technology that we still use daily. But did you know that it was actually a re-branded Stratasys uPrint? (inventor of FDM technology).
On the other hand, the Replicator was Makerbot's first "mini printer", it is filament-based itself, but it championed the open source movement and was offered as a kit. We remember the buzz about it at the time, so much so that the project sparked the interest of Stratasys, which subsequently acquired the start-up. Makerbot is still the go-to brand for the educational segment and is now part of the new UltiMaker ecosystem, to be unveiled early next year.
We have witnessed a revolution and, after all these years, we are anything but tired of finding out what the AM market has in store for us in the near future!
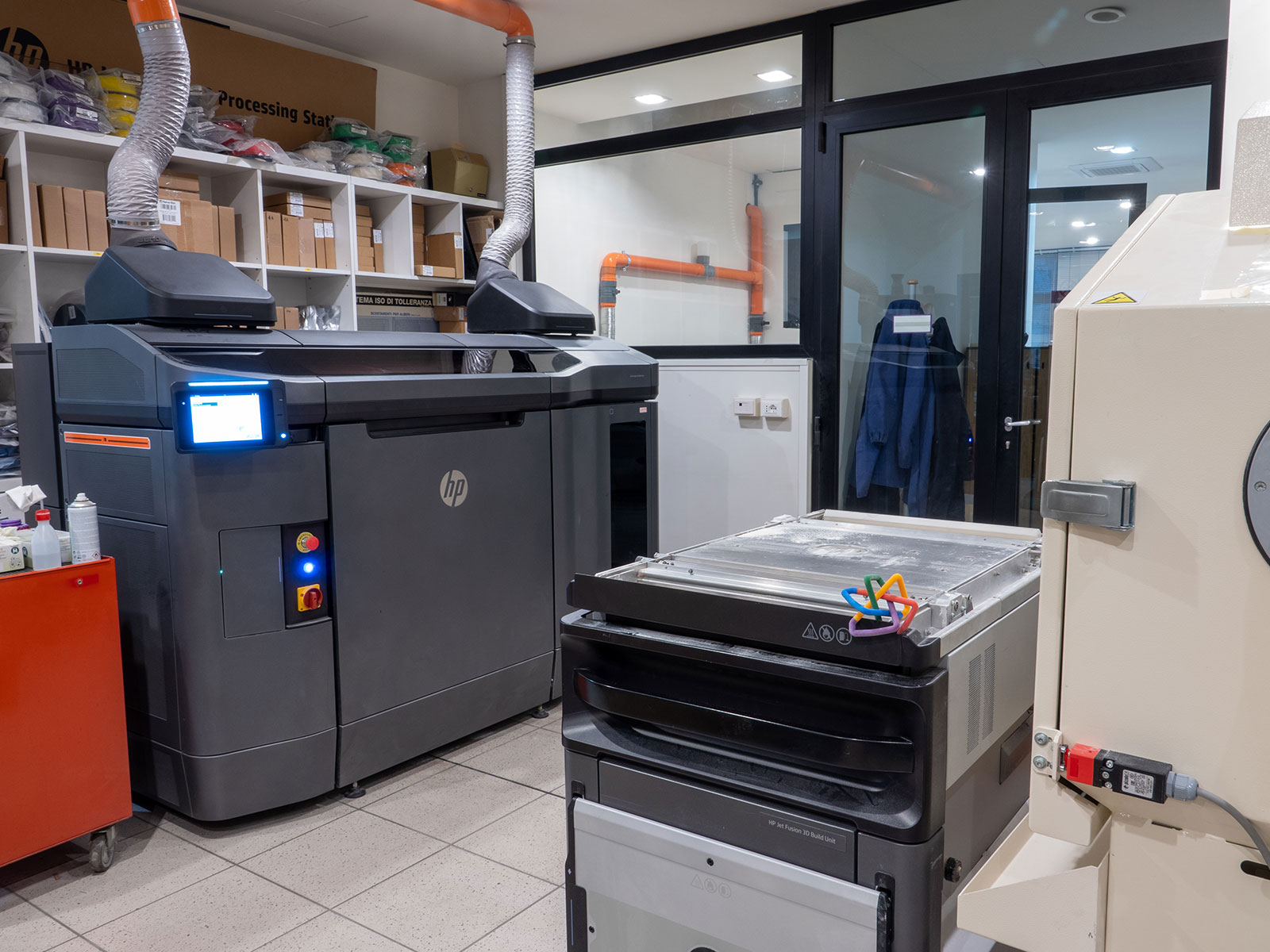
And the story goes on...
The short window of time between the fall of 2016 and the fall of the following year was the timeframe that indisputably set the direction of additive manufacturing: the new goal was production.
There are two key events:
- HP launches Multi Jet Fusion technology
- GE acquires Concept Laser and Arkam
The two corporations took a stand in the industry and determined that the future of additive manufacturing would be not only in rapid prototyping, but also in series production and the manufacturing of critical components.
It was exactly 5 years ago, halfway through our journey, that we were early adopters of HP’s Multi Jet Fusion and made it available to designers, thus giving them the possibility to exploit the advantages of additive manufacturing even for batches with quantities nearing mass production.
Carbon was not long in coming. Along with it came the possibility of combining high-performance materials with repeatability. To get ahead of the times we welcomed the challenge of investing in Carbon Digital Light Synthesis technology, even during a difficult time like 2020: a year that saw us all dealing with the uncertainty of the global pandemic.
Juno, for the past 10 years, has been investing to test the extreme to which any combination of technology and material can be pushed, and will continue to do so by relying on its 5 souls - J 3DPRINT, J-DESIGN, J-R&D, J-SALES, J-FUTURE - which, together, can offer partners access to a multifaceted experience with practical support, from idea to production.